Unlocking the Potential of Hydraulic Split Flange Caps in Modern Business
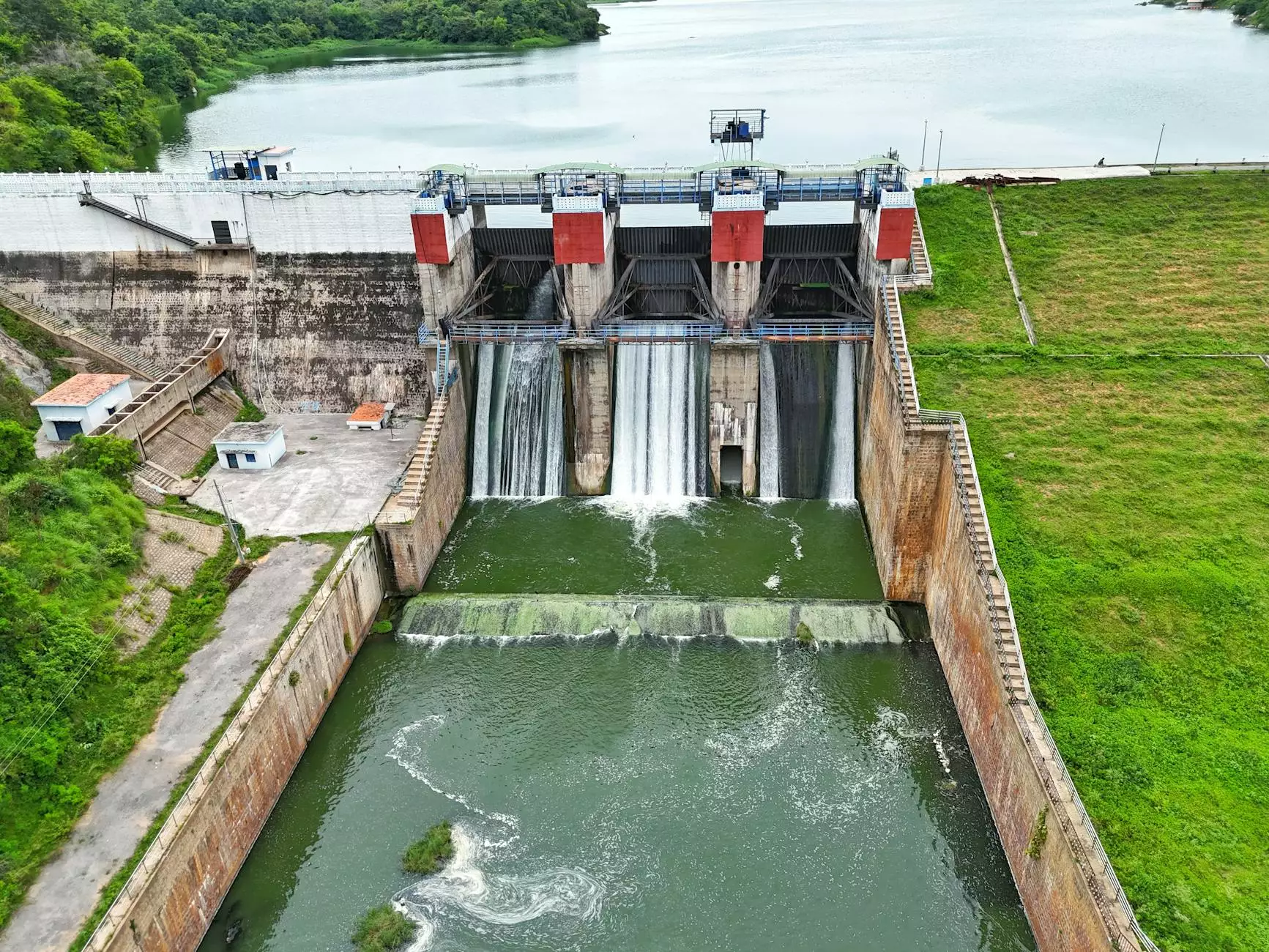
In today’s fast-paced industrial landscape, businesses are constantly seeking innovative solutions to enhance operational efficiency and reliability. One such product that plays a crucial role in maintaining the integrity of hydraulic systems is the hydraulic split flange cap. Understanding the applications, benefits, and future trends of these caps can empower organizations to make informed decisions about their hydraulic systems, ensuring they operate at optimal levels.
What Are Hydraulic Split Flange Caps?
Hydraulic split flange caps are specialized components designed to cover and seal the ends of hydraulic flanges. They are crucial for preventing contamination and ensuring the safe operation of hydraulic systems. These caps are engineered to withstand high pressure and extreme temperatures, making them essential in various industrial applications.
Key Features of Hydraulic Split Flange Caps
- Durability: Made from high-quality materials such as stainless steel and durable plastics, these caps are built to last.
- High Pressure Resistance: They can withstand significant pressure, essential for maintaining the integrity of hydraulic systems.
- Temperature Tolerance: Capable of performing in a wide range of temperatures, from freezing cold to extreme heat.
- Easy Installation: Designed for user-friendly application, allowing for quick assembly and disassembly.
- Versatility: Suitable for various fluid types and industries, including construction, manufacturing, and automotive.
Applications of Hydraulic Split Flange Caps
The versatility of hydraulic split flange caps extends across numerous industries. Here are some notable applications:
A. Construction Industry
The construction sector heavily relies on hydraulic equipment, such as excavators and bulldozers. Hydraulic split flange caps ensure that these heavy machines operate smoothly by preventing leaks and contamination in hydraulic circuits.
B. Manufacturing
In manufacturing processes, hydraulic systems are utilized for automation and material handling. The use of hydraulic split flange caps minimizes maintenance costs and downtime by protecting hydraulic lines from dirt and moisture.
C. Automotive Sector
In automotive applications, hydraulic systems are crucial for power steering, braking, and suspension. Implementing these caps within systems protects sensitive components, thereby enhancing safety and performance.
D. Agricultural Machinery
Agricultural equipment like tractors and harvesters use advanced hydraulic systems. The reliability provided by hydraulic split flange caps ensures that farmers can depend on their machinery in demanding conditions.
Benefits of Using Hydraulic Split Flange Caps
The adoption of hydraulic split flange caps in various applications comes with numerous advantages. Below are some of the key benefits:
A. Enhanced System Integrity
By sealing hydraulic flanges, these caps significantly reduce the risk of leaks and contamination. This enhances the overall integrity of hydraulic systems.
B. Cost-Effective Maintenance
By preventing leaks and contamination, hydraulic split flange caps reduce the need for frequent replacements and repairs, resulting in lower long-term costs.
C. Safety Assurance
With reduced risk of hydraulic fluid leaks, businesses can provide a safer working environment for their employees, minimizing hazards associated with hydraulic failures.
D. Improved Performance
Sealed hydraulics operate more efficiently, leading to better performance of machinery and equipment. This increase in performance translates to higher productivity levels.
Choosing the Right Hydraulic Split Flange Caps
When selecting hydraulic split flange caps for your systems, several factors must be considered to ensure compatibility and performance:
A. Material Selection
Choosing the right material is critical. Consider factors like chemical compatibility, temperature tolerance, and environmental conditions. For high-pressure applications, stainless steel caps may be better suited, while plastic options may suffice for less demanding tasks.
B. Size and Specifications
It is vital to select caps that fit your specific hydraulic flanges. Accurate measurements of diameter and flange dimensions will ensure proper sealing and optimal performance.
C. Quality Assurance
Opt for caps produced by reputable manufacturers, such as Fitsch.cn, which emphasizes quality and reliability in their products.
Future Trends in Hydraulic System Components
The evolution of hydraulic systems is ongoing, and several trends are shaping the future of hydraulic split flange caps:
A. Emphasis on Sustainability
As industries move towards eco-friendly practices, manufacturers are increasingly using sustainable materials for hydraulic components, including split flange caps.
B. Technological Integration
With the rise of Industry 4.0, integrating smart technologies into hydraulic systems is becoming prevalent. Future hydraulic split flange caps may include sensors for monitoring pressure and temperature, providing real-time data to operators.
C. Customization
As various industries have distinct needs, the demand for customizable hydraulic split flange caps is rising. Tailored solutions will enhance functionality and efficiency.
Conclusion
In summary, hydraulic split flange caps are indispensable components in modern hydraulic systems. Their role in enhancing performance, safety, and efficiency cannot be overstated. As industries continue to evolve, the demand for high-quality hydraulic components will only grow. Companies like Fitsch.cn are at the forefront of this evolution, providing reliable solutions that meet the diverse needs of businesses worldwide.
Investing in top-notch hydraulic systems, including hydraulic split flange caps, is essential for any business aiming to thrive in today’s competitive landscape. Embrace these advanced solutions and watch your operational efficiency soar!