Investment Molding Process for Metal Fabricators and 3D Printing
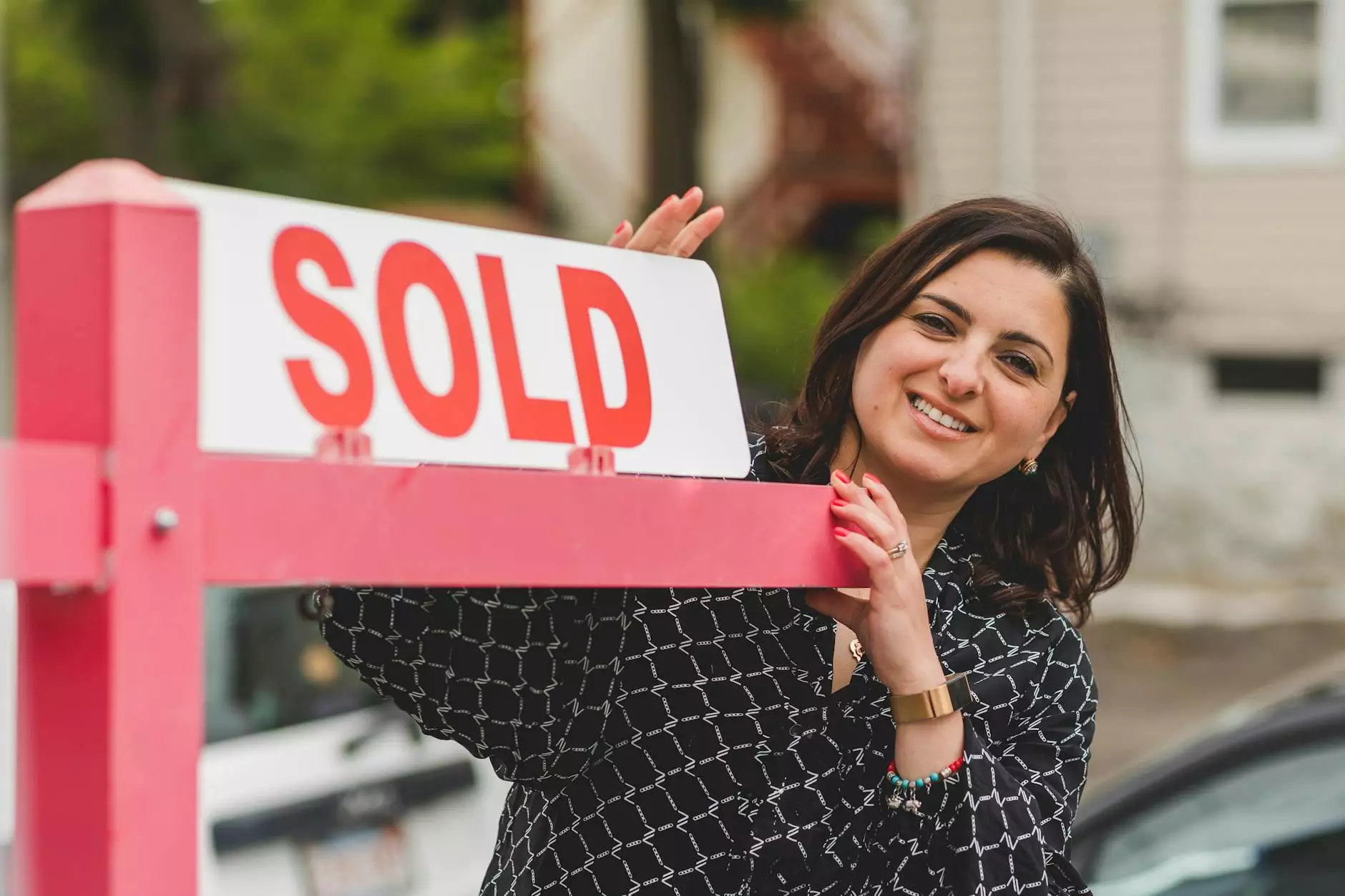
Welcome to QuickParts.com, your go-to resource for all things related to metal fabrication and 3D printing. In this article, we will explore the investment molding process, its benefits, applications, and the step-by-step procedure involved. Whether you are a metal fabricator or involved in 3D printing, this comprehensive guide will provide you with valuable insights.
What is Investment Molding?
Investment molding, also known as lost-wax casting, is a highly versatile and precise manufacturing process used in metal fabrication and 3D printing. It involves creating intricate and complex metal parts by using a refractory material mold. The process is called investment molding because the mold is created by investing a pattern made of wax or other materials. This pattern is then removed, creating a cavity that is filled with molten metal material to form the final product.
Benefits of Investment Molding
Investment molding offers numerous benefits for both metal fabricators and those in the 3D printing industry. Some of the key advantages include:
- Precision: Investment molding allows for the production of highly accurate and intricate parts with tight tolerances, ensuring high-quality end products.
- Design Freedom: This process enables the creation of complex geometries and intricate details that may be challenging to achieve using other manufacturing methods.
- Material Versatility: Investment molding supports a wide range of materials, including various metals, alloys, and even ceramic materials, offering versatility in material selection for different applications.
- Cost-Efficiency: While investment molding may involve several steps, it can be cost-effective for producing small to medium quantities of parts compared to conventional manufacturing methods.
- Surface Finish: The investment molding process provides excellent surface finish options, reducing the need for additional finishing treatments and improving the overall aesthetics of the final product.
Applications of Investment Molding
Investment molding finds applications across various industries, including:
- Aerospace and Defense: Investment molding is widely used in aerospace and defense industries due to its ability to create lightweight and intricate parts necessary for aircraft and defense systems.
- Medical: The medical field benefits from investment molding for producing medical equipment, implants, and prosthetics with high precision and biocompatible materials.
- Jewelry: Jewelry designers and manufacturers utilize investment molding to create intricate and one-of-a-kind jewelry pieces that exhibit superior detail and quality.
- Automotive: Investment molding plays a crucial role in the automotive industry, enabling the production of complex engine components, turbochargers, and other critical parts with exceptional strength and durability.
- Prototyping: Rapid prototyping using investment molding allows for quick turnaround times, cost-effective iterations, and the validation of product designs before proceeding with full-scale production.
The Investment Molding Process
The investment molding process involves several key steps:
- Pattern Creation: The process begins with the creation of a pattern, which can be made of wax, plastic, or other materials. The pattern represents the desired shape of the final part.
- Assembly: The pattern is attached to a gating system, which includes channels for the molten metal to flow and vents for air and gases to escape during the casting process.
- Investment: The pattern assembly is coated with a ceramic shell material called the investment. This investment layer ensures the surface quality and dimensional accuracy of the final part.
- Burnout: The coated pattern is heated, causing the pattern to melt and combust, leaving behind an empty cavity in the investment mold.
- Casting: Once the mold is prepared, molten metal material is poured into the cavity and allowed to solidify. The metal fills the cavity, taking the shape of the original pattern.
- Finishing: After solidification, the investment shell is removed, and the casting is cleaned, removing any remaining investment material and performing necessary finishing operations such as grinding, polishing, or heat treatment.
Conclusion
Investment molding, also known as lost-wax casting, is a highly versatile and precise manufacturing process used in metal fabrication and 3D printing. It offers numerous benefits, including precision, design freedom, material versatility, cost-efficiency, and excellent surface finish. The process finds applications in various industries such as aerospace, defense, medical, jewelry, automotive, and prototyping. Understanding the investment molding process and its applications can lead to innovative and high-quality solutions for metal fabricators and those in the 3D printing industry.
For an extensive range of investment molding services and top-quality results, visit QuickParts.com today!