Understanding the Role of China Precision Injection Mould Suppliers
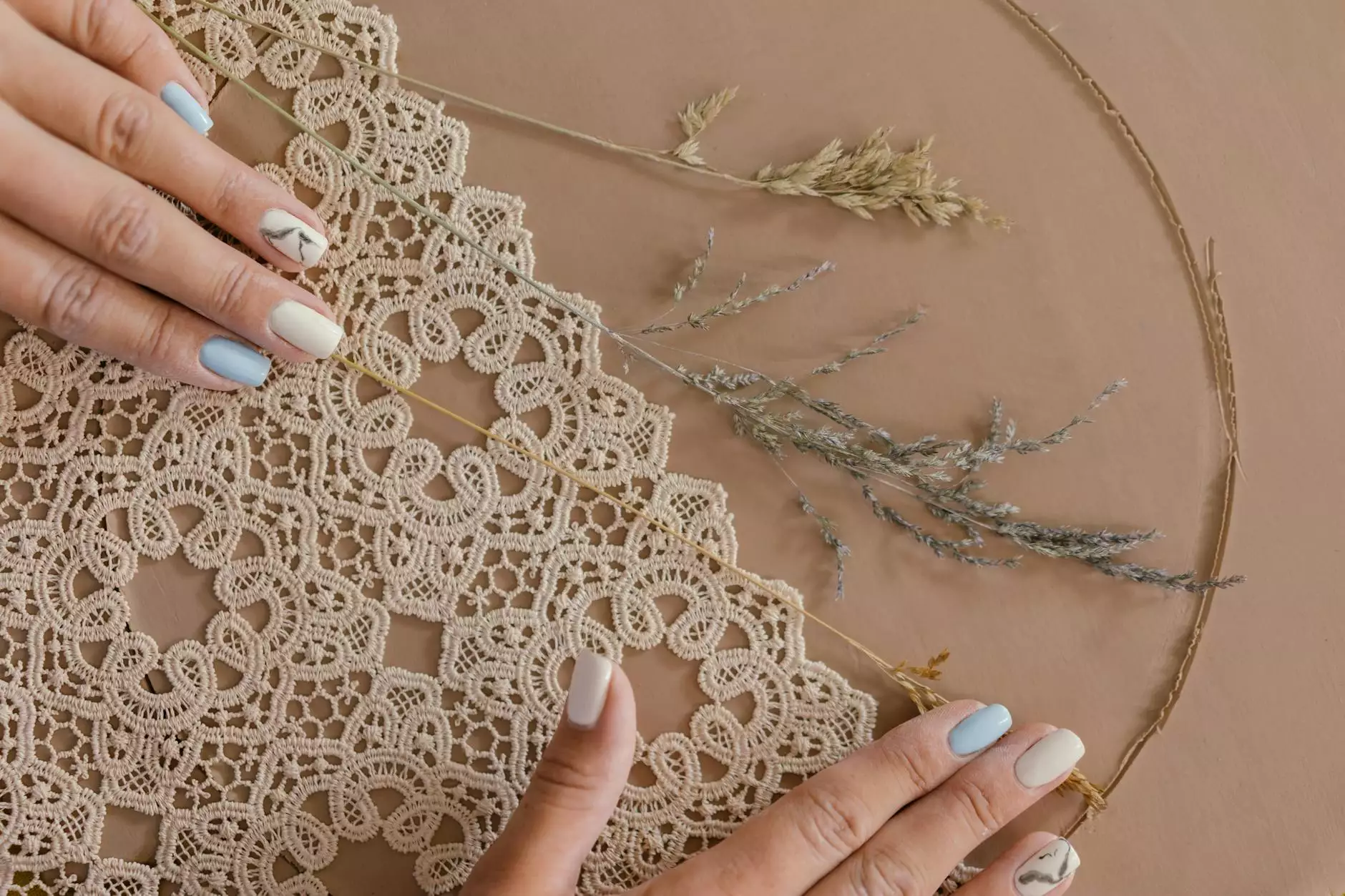
In today’s competitive manufacturing landscape, China precision injection mould suppliers have emerged as key players in providing high-quality solutions across various industries. These suppliers excel in creating precise, durable, and versatile moulds that are critical to the production of a wide range of components. Their expertise not only optimizes productivity but also significantly reduces operational costs for manufacturers worldwide.
The Significance of Precision Injection Moulding
Precision injection moulding is a highly sophisticated manufacturing process used to produce intricate shapes in various materials. In this section, we will explore what makes this process beneficial and how it contributes to various industries.
1. High Level of Accuracy
One of the primary advantages of precision injection moulding is its ability to produce parts with exceptional accuracy. This process allows manufacturers to:
- Maintain Tight Tolerances: Achieve dimensions within +/− 0.01mm, which is essential for fitting components perfectly in automotive, aerospace, and electronic applications.
- Enhance Product Quality: Improve surface finishes and reduce defects, thus increasing overall product reliability and consumer satisfaction.
2. Versatility in Materials
Another noteworthy feature of precision injection moulding is the range of materials that can be utilized. Suppliers in China offer moulds for:
- Thermoplastics: Such as ABS, PVC, and polycarbonate, which are common in consumer goods.
- Thermosetting Plastics: Ideal for high-heat applications.
- Metals: Moulds can also be designed for metal injections, broadening the scope of applications.
3. Cost-Effectiveness
By establishing a partnership with China precision injection mould suppliers, manufacturers can significantly lower their production costs due to:
- Economies of Scale: Mass production reduces per-unit costs.
- Reduced Waste: Advanced technology minimizes material waste during the injection moulding process.
Choosing the Right Supplier
Selecting the right precision injection mould supplier in China is pivotal for achieving manufacturing success. Here are important factors to consider when making your choice:
1. Industry Reputation
Research the supplier's track record and customer reviews. A well-established supplier with positive feedback can provide peace of mind and assurance of high-quality products.
2. Technical Expertise
Evaluate the technical capabilities of the supplier. Expertise in the latest technological advancements in mould fabrication, such as:
- 3D Printing: For rapid prototyping.
- CNC Machining: Enhanced precision.
3. Quality Assurance Processes
Ensure that the supplier implements stringent quality assurance and control measures. Look for:
- ISO Certifications: Such as ISO 9001 indicating adherence to international quality standards.
- Regular Audits: Conducting internal and external audits to maintain quality levels.
Advantages of Partnering with DeepMould
When considering options for precision injection moulding, DeepMould stands out among the array of China precision injection mould suppliers. Here’s why:
1. Comprehensive Services
DeepMould offers an extensive range of services, ensuring that all your manufacturing needs are met under one roof. From design and prototyping to finishing and assembly, they cover every aspect of the injection moulding process.
2. Experienced Team
The team at DeepMould consists of seasoned professionals with vast experience in the industry. Their expertise enables them to solve complex problems efficiently and effectively, providing personalized support throughout the whole process.
3. State-of-the-Art Machinery
Utilizing the latest machinery and technology allows DeepMould to produce high-quality moulds with enhanced precision. This investment in technology translates to:
- Faster Turnaround Times: Streamlining the production process without compromising quality.
- Improved Design Capabilities: Capability to handle intricate designs and large volumes.
Environmental Considerations in Injection Moulding
As global awareness regarding sustainability increases, it is essential for China precision injection mould suppliers to adopt environmentally friendly practices. Here’s how companies can ensure their processes are eco-friendly:
1. Sustainable Materials
Opting for sustainable materials such as biodegradable plastics can significantly lower the environmental impact of moulding. Suppliers should aim to use:
- Recycled Plastics: Helping to reduce waste and promote a circular economy.
- Biodegradable Options: These materials can decompose naturally and minimize pollution.
2. Energy-Efficient Practices
Implementing energy-efficient practices during production can reduce carbon footprints. Practices include:
- Using Energy Star Equipment: Reduces energy consumption in machinery.
- Improving Process Efficiency: Streamlining operations to use less energy through lean manufacturing techniques.
3. Waste Management
Proper waste management strategies are vital in injection moulding industries. Suppliers should focus on:
- Recycling Scrap Materials: Reintegrating waste materials for new production.
- Reducing Emissions: Employing measures to minimize emissions during manufacturing.
Future Trends in Precision Injection Moulding
As technology continues to advance, so too does the world of injection moulding. Here are emerging trends that may shape the future of this industry:
1. Automation and Robotics
Increasing automation in manufacturing processes is expected to enhance productivity while reducing labor costs. Robotics will play a crucial role by:
- Automating Repetitive Tasks: Reducing human error.
- Improving Safety: Minimizing risks associated with manual handling.
2. Smart Manufacturing
The integration of IoT (Internet of Things) technology into injection moulding processes facilitates smart manufacturing. This allows for:
- Real-Time Monitoring: Optimizing machine performance.
- Predictive Maintenance: Preventing downtime through early fault detection.
3. Innovative Materials
As research and development continue, the availability of innovative materials will expand, allowing for greater flexibility and capability in mould construction. Future materials may include:
- Composite Materials: Improving strength and lightweight properties.
- Advanced Polymers: Offering unique thermal and chemical resistance characteristics.
Conclusion
In conclusion, partnering with China precision injection mould suppliers is instrumental for businesses seeking to enhance their manufacturing capabilities. Through their advanced technology, rigorous quality assurance, and commitment to sustainability, these suppliers provide invaluable solutions that drive efficiency, reduce costs, and support innovation. By choosing reputable suppliers like DeepMould, companies can secure a competitive edge in today’s fast-paced market.
As the manufacturing landscape evolves, it is crucial to keep pace with emerging trends to not only remain relevant but to excel in your industry. The future of precision injection moulding is bright, filled with opportunities for those who embrace advancements and foster strong partnerships.