Tooling for Injection Molding: A Comprehensive Guide for Metal Fabricators
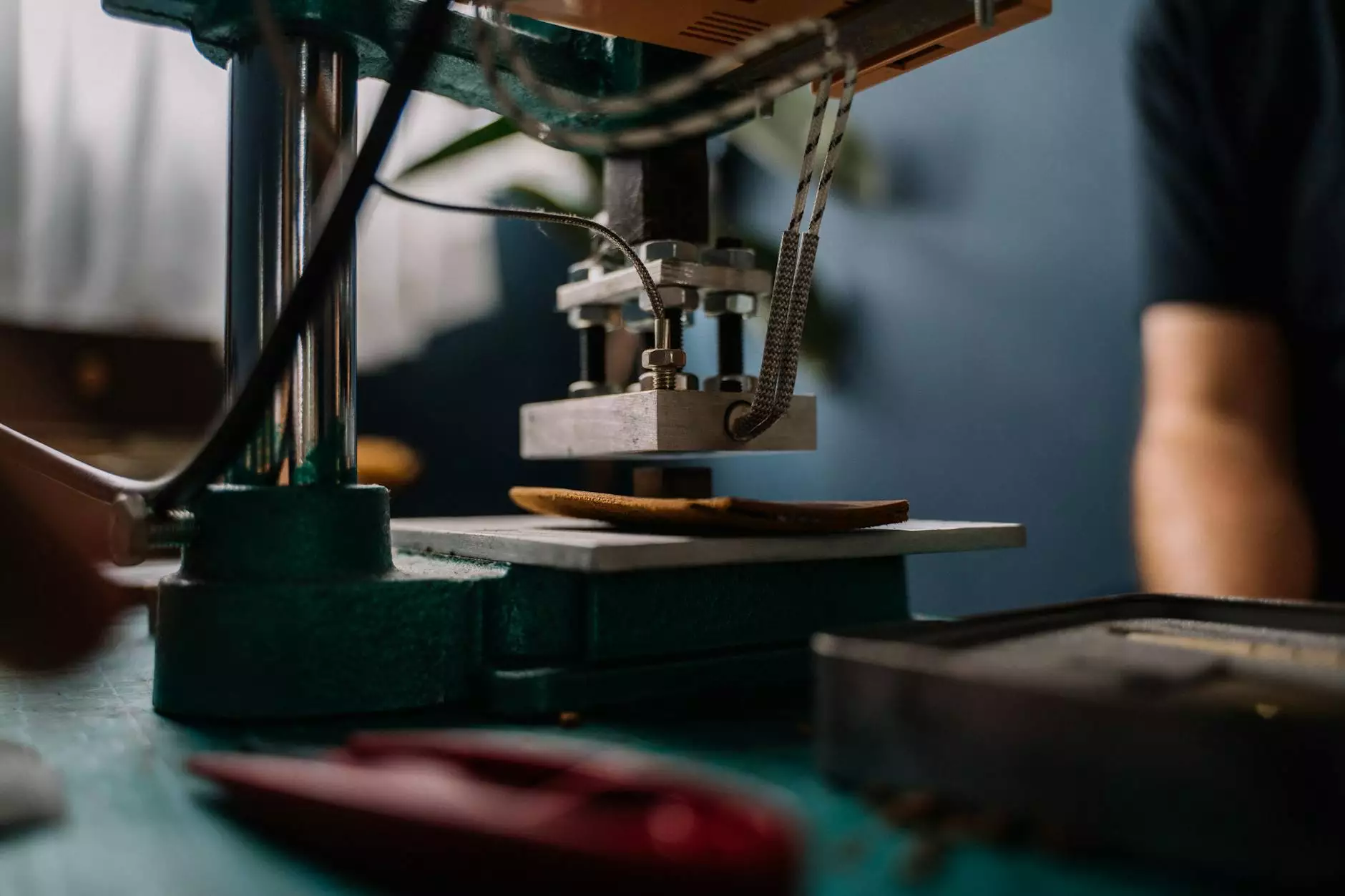
Tooling for injection molding plays a crucial role in the world of manufacturing, especially for businesses focused on producing high-precision components. Understanding the basics of tooling not only enhances production efficiency but also ensures superior product quality. This article delves into the intricate details of injection molding tooling, its types, benefits, design considerations, and its significance for metal fabricators.
What is Injection Molding Tooling?
At its core, tooling for injection molding involves creating molds that shape liquid plastics into specific forms as they cool. This manufacturing process is vital for producing an array of products, from consumer goods to complex automotive components. By using specific molds, manufacturers can achieve both mass production and cost-efficiency.
The Importance of Tooling in Injection Molding
For manufacturers, especially those in the realm of metal fabricators, the quality of the tooling directly impacts:
- Product Quality: Superior tooling results in precise dimensions and surface finishes.
- Production Efficiency: Quality molds reduce cycle times and wastage.
- Cost-Effectiveness: Effective tooling minimizes the need for rework and maximizes resource utilization.
Types of Injection Molding Tooling
Understanding the different types of tooling available can help fabricators select the right option for their needs. Here are the main types:
1. Single Cavity Molds
As the name suggests, these molds are designed to produce one part per cycle. They are ideal for small production runs or prototyping, as they are typically less expensive to manufacture.
2. Multi-Cavity Molds
These molds can produce multiple parts in a single cycle, increasing efficiency and reducing per-part costs. Multi-cavity molds are great for high-volume production but require more complex designs.
3. Family Molds
Family molds allow for the production of different parts simultaneously. This approach balances the need for varied components while maintaining efficiency.
4. Hot Runner Molds
Using a hot runner system keeps the plastic in a molten state as it moves through the mold, enhancing cycle times and reducing waste. These systems can significantly improve efficiency and are beneficial for larger operations.
5. Cold Runner Molds
These molds use a simpler design, where plastic cools in the runner system as well, leading to more waste. However, the lower initial investment makes them attractive for smaller runs.
Materials Used in Injection Molding Tooling
The material selection for tooling for injection molding significantly influences cost, durability, and performance. Here are some common materials:
- Steel: Known for its strength and durability, it is excellent for high-volume production but comes at a higher cost.
- Aluminum: Lightweight and less expensive, aluminum is suitable for lower volume runs and prototyping but may wear out quicker than steel.
- Brass: Often used for intricate mold components requiring high precision, brass can be an effective choice for certain applications.
Design Considerations for Tooling
When designing tooling for injection molding, various factors are essential for ensuring high-quality results:
1. Part Design
The complexity of the part design can significantly affect tooling. Considerations should include draft angles, wall thickness, and features such as undercuts.
2. Tolerances and Specifications
Identifying the required tolerances and specifications at the outset is crucial for ensuring that the tooling meets production requirements.
3. Cooling Systems
Incorporating an effective cooling system within the tooling can dramatically reduce cycle time and improve efficiency. Designs must consider the placement and flow of cooling channels.
4. Maintenance and Durability
Tooling should be designed not only for immediate production needs but also for long-term maintenance requirements and durability under repetitive use.
The Benefits of Effective Tooling for Injection Molding
Investing in high-quality tooling for injection molding can yield numerous benefits, particularly for metal fabricators:
- Increased Production Rates: Efficient tooling results in faster production cycles, which means more output in less time.
- Cost Reduction: While the initial investment may be higher, quality tooling leads to lower operational costs over time.
- Improved Quality Control: High-quality molds lead to consistent product quality, reducing defects and waste.
Conclusion: Elevating Your Manufacturing Process
In the highly competitive world of manufacturing, particularly in industries served by metal fabricators, understanding the fundamentals of tooling for injection molding can provide a considerable advantage. Choosing the right type of tooling, utilizing appropriate materials, and focusing on thoughtful design can elevate your production processes, ensuring high-quality outputs and efficient operations. At DeepMould.net, we specialize in providing high-quality tooling solutions tailored to meet the unique needs of our clients in the metal fabrication industry. Invest in the right tooling today, and watch your manufacturing capabilities flourish.