Transforming Metal Fabrication with Rapid 3D Prototyping: The Future of Manufacturing at DeepMould
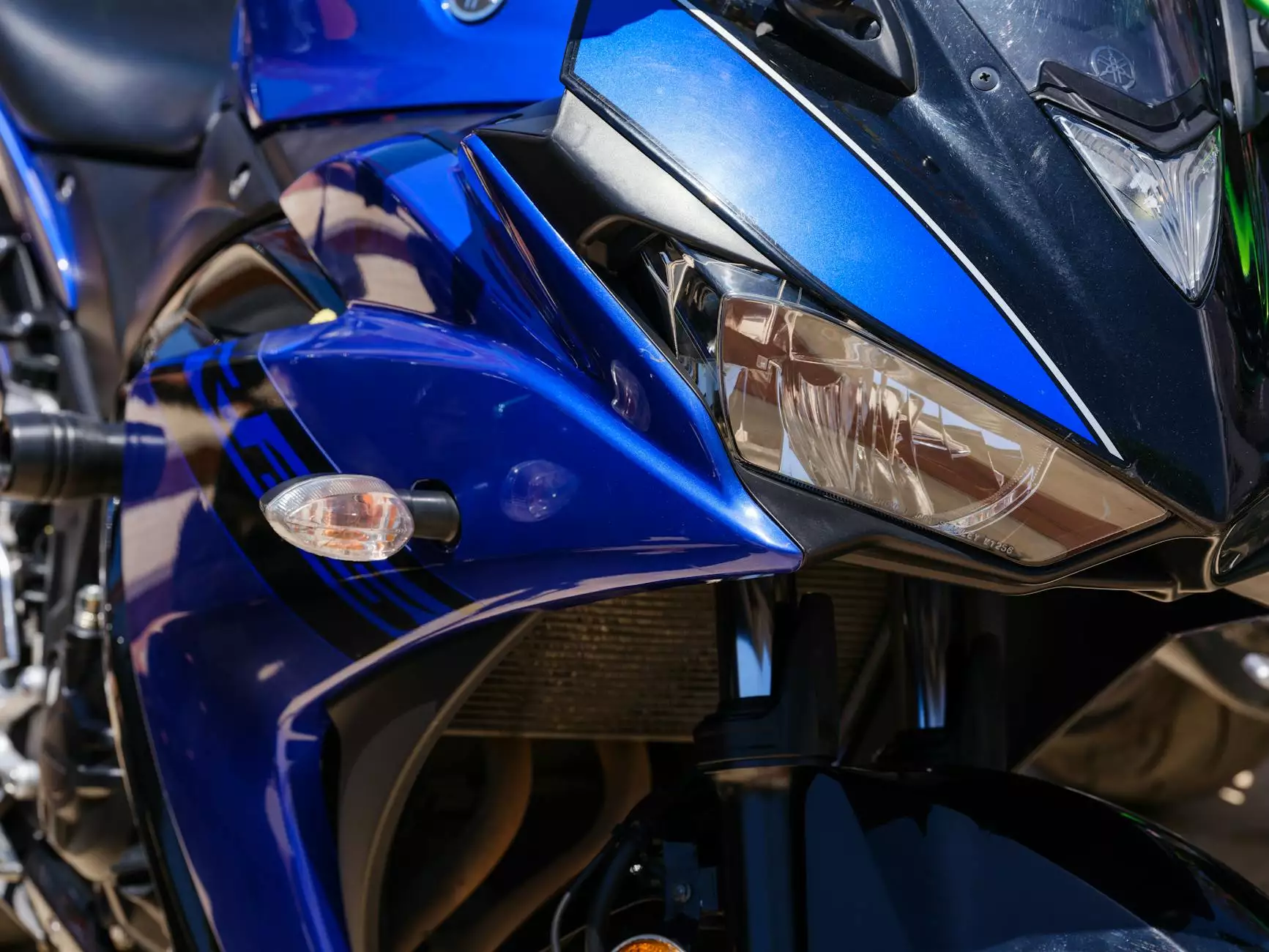
In the fast-evolving landscape of modern manufacturing, rapid 3d prototyping stands out as a pivotal technology, revolutionizing how metal fabricators approach design, production, and innovation. As companies seek faster turnaround times, higher precision, and cost-effective solutions, embracing rapid 3d prototyping offers unmatched advantages, positioning businesses like DeepMould at the forefront of the industry.
Understanding Rapid 3D Prototyping: The Cornerstone of Modern Metal Fabrication
At its core, rapid 3d prototyping is a manufacturing process that uses digital 3D models to quickly create physical prototypes, models, or components with minimal lead times. This technology employs advanced additive manufacturing techniques, such as metal 3D printing, to produce highly detailed, complex, and functional parts directly from CAD files. In the context of metal fabricators, this means that intricate metal prototypes and components can be realized faster and more accurately than traditional methods.
The Evolution of Metal Fabrication Through Rapid 3D Prototyping
Historically, metal fabrication relied heavily on subtractive processes like machining, casting, and welding. While effective, these processes are often time-consuming, resource-intensive, and limited in complexity. The advent of rapid 3d prototyping has fundamentally altered this paradigm by enabling:
- Rapid iteration and testing: Designers can iterate prototypes quickly to refine function and aesthetics.
- Design freedom: Create complex geometries impossible with traditional methods, including internal channels, lattice structures, and customized components.
- Cost reduction: Minimize material waste and reduce labor costs through streamlined workflows.
- Accelerated time-to-market: Bring innovative products to market faster, gaining a competitive edge.
Key Technologies in Rapid 3D Prototyping for Metal Fabrication
The technological backbone of rapid 3d prototyping in the metal industry involves several advanced methods, each suited for specific applications:
Selective Laser Melting (SLM)
SLM involves using a high-powered laser to selectively fuse powdered metal particles layer by layer, creating dense and durable metal parts. It allows for complex geometries and high-quality surface finishes, essential for functional prototypes and end-use components.
Direct Metal Laser Sintering (DMLS)
DMLS is similar to SLM but typically employs different laser parameters and powders. It produces high-precision, intricate metal parts suitable for aerospace, automotive, and industrial applications.
Electron Beam Melting (EBM)
EBM uses an electron beam in a vacuum environment to melt metal powders. It provides exceptional strength and is often used for medical implants and aerospace components where material integrity is critical.
Binder Jetting and Metal 3D Printing
This innovative process uses a binder to adhere metal powders into pre-designed shapes, which are then sintered or infiltrated with metal alloy for strength, enabling rapid scale-up production of prototypes and small batches.
Advantages of Rapid 3D Prototyping for Metal Fabricators
Implementing rapid 3d prototyping techniques offers numerous benefits that can elevate the capabilities of metal fabricators like DeepMould:
- Unmatched Precision and Detail: Achieve highly detailed prototypes with tight tolerances required in specialized industries, including aerospace, automotive, and healthcare.
- Design Flexibility: Bring innovative, complex geometries to life without the constraints of traditional manufacturing limits like tooling or molds.
- Speed of Production: Drastically reduce prototyping lead times from weeks to days, enabling quicker design validation and iteration.
- Material Versatility: Use a range of metals such as stainless steel, titanium, aluminum, and cobalt-chromium, tailored to the specific needs of each project.
- Reduced Costs: Minimize material waste and eliminate expensive tooling costs, making small-batch manufacturing economically viable.
- Risk Mitigation: Test prototypes under real-world conditions before committing to full-scale production, reducing costly design errors.
Why DeepMould Is a Leader in Rapid 3D Prototyping for Metal Fabrication
DeepMould.net has positioned itself as a premier metal fabricator that harnesses the power of rapid 3d prototyping to deliver innovative solutions. Their cutting-edge facility combines the latest additive manufacturing technologies with expert craftsmanship to help businesses push boundaries and accelerate their development cycles.
Industry-Leading Technology and Expertise
DeepMould invests in state-of-the-art SLM, DMLS, and EBM systems, ensuring high precision, repeatability, and material availability. Their team of engineers and technicians possesses extensive experience in translating complex designs into functional prototypes, adhering to the highest standards of quality and durability.
Tailored Solutions for Diverse Industries
From aerospace components requiring stringent tolerances to intricate jewelry molds, DeepMould adapts its rapid 3d prototyping services to meet specific industry demands. This flexibility allows clients to innovate faster and reduce time-to-market.
End-to-End Service Suite
Beyond prototyping, DeepMould offers comprehensive services, including design consultation, simulation, post-processing, and small-batch production. This seamless integration streamlines workflows and ensures clients receive ready-to-use components for testing, presentation, or final deployment.
Implementing Rapid 3D Prototyping in Your Metal Fabrication Workflow
To maximize the benefits of rapid 3d prototyping, companies should consider strategic integration into their existing processes:
- Design Optimization: Leverage CAD and simulation tools alongside prototyping to refine geometries and ensure manufacturability.
- Material Selection: Choose appropriate metals based on mechanical properties, corrosion resistance, and application requirements.
- Prototype Testing: Use prototypes to conduct functional testing, validate fit and form, and gather user feedback.
- Iterative Development: Rapidly produce successive versions to improve design and performance efficiently.
- Transition to Production: Use insights from prototypes to develop molds or proceed directly with small-batch manufacturing, reducing overall project timelines.
Future Trends of Rapid 3D Prototyping in Metal Fabrication
The horizon of rapid 3d prototyping in the metal industry is continually expanding with innovations such as:
- Hybrid Manufacturing: Combining additive and subtractive processes for optimal surface finish and structural integrity.
- AI-Driven Design for Additive Manufacturing: Utilizing artificial intelligence to create optimized geometries and support structures, reducing waste and enhancing performance.
- Cloud-Based Collaboration: Enhancing remote design prototyping and real-time collaboration across global teams.
- Sustainable Manufacturing: Developing eco-friendly materials and processes to minimize environmental impact, aligning with green manufacturing goals.
Conclusion: Embracing the Power of Rapid 3D Prototyping for Competitive Advantage in Metal Fabrication
In summary, rapid 3d prototyping is not just a technological advancement; it is a strategic enabler for modern metal fabricators seeking to innovate, optimize, and lead in their respective markets. Companies like DeepMould are exemplifying how leveraging these advanced capabilities can dramatically shorten development cycles, enhance product quality, and drive business growth. As industries continue to evolve and demand more complex, precise, and efficient manufacturing solutions, integrating rapid 3d prototyping becomes essential for staying ahead of the competition.
By embracing this transformative technology, metal fabrication businesses can unlock new possibilities, deliver superior products, and meet the ever-growing expectations of their clients. The future of manufacturing is here, and rapid 3D prototyping at DeepMould is leading the way to a smarter, faster, and more sustainable industry.